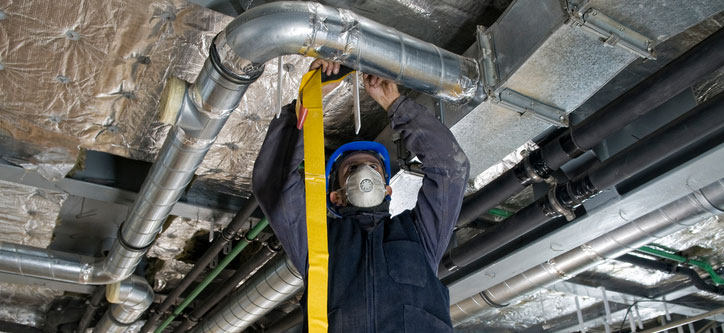
HVAC Installation
The kind of work HVAC installers do can range from a relatively simple drop-in replacement of a split-system heat pump unit on a suburban house… to a major steam plant replacement in a hospital basement… to a full install in a newly constructed LEED (Leadership in Energy and Environmental Design) Gold certified green building with passive solar heating, computer-controlled shading and mixed-mode night flushing systems.
Installation specialists are found on both the residential and commercial side of the business. Many larger contracting companies bid jobs on both sides, but installers working for them will tend to specialize in one or the other since the equipment, system design and applications are so different.
Installers have to be comfortable with hard physical labor and heavy equipment and tools since they have to lift, carry, and maneuver major system components into place. An install could involve everything from a crane for a commercial rooftop install to a common sabre saw and tin snips for cutting sheet metal.
In many cases, installers also have to serve as designers. Major installations on commercial projects will be specced out by engineers, but on small commercial replacement projects or residential installs, it is up to the installer to survey the site, make the correct calculations for volume and BTU requirements, and then recommend the right equipment and layout to meet the need.
“You become more or less like an engineer,” says one thirty-year veteran refrigeration mechanic we talked to. Evaluating the system load and choosing the proper equipment keeps gear from getting overstressed and failing prematurely.
Installers can face a lot of grief because of this responsibility. Service technicians love to blame the guy who put in the package any time there is a problem. So there is very little room for error when working in HVAC installation.
Energy-Optimizing Technology Makes Sense Financially
When an HVAC system breaks, it has to be fixed, but unlike repairs, a new installation can usually be scheduled, and that only happens when there is an economic advantage to doing it.
According to 26-year industry veteran Mike DeRicco, “You know, everybody’s trying to get the power consumption down, so just about every aspect of a machine has changed. All the motors are high-efficient motors, you have high-efficient gas burners in them. They now have variable frequency drives on the motors, so now the speed of the motors can ramp up and down, so that it uses less energy when it can as opposed to running at 100 percent all day long like years ago.”
Those changes drive a lot of the work that installers do today. The efficiency can save thousands of dollars over time, which makes big-ticket installations or replacements well worth the money that goes into them initially.
Installation Includes Both New Construction and Retrofits on Old Buildings
You might think installation work sounds like you are getting to start with a blank slate, but that’s only the case with new construction. Even in those cases, you will frequently be constrained in your options by the building design the engineers and architects laid out.
Elsewhere, installation work has to fit in existing spaces and often work with existing ductwork and distribution systems. You might be ripping everything out and reinstalling from scratch, but such major projects are rare. More common are piecemeal updates for a new control system or a smart ducting installation.
But installers understand that they need to work within the totality of the system. Conducting airflow analyses and running the numbers on system sizing are important steps in evaluating whether or not a distribution system can even handle a new or larger unit.
Even Installation Includes a Little Service Work
Being an installer doesn’t get you out of performing basic troubleshooting work, though. Once you get a system in place, you don’t just walk away: you need to have it running and meeting all the right benchmarks, or you’re going to have some pretty unhappy customers. So fine-tuning and some basic service work will also be in the cards for new system installations.
The benefit is that you are working with equipment that you just put in yourself, so it’s a lot easier than running down problems in an install that someone else did 20 years ago and forgot to document.
The Hours Are Usually Predictable, the work isn’t
In an industry that almost always requires some after-hours, on-call work to handle emergencies, installers can usually head in at 8 a.m. and hang their hard hats up at 5 p.m. to go home for dinner with the family. The phone won’t ring after hours.
This doesn’t mean overtime isn’t an option. On a big job with a tight schedule, 70-hour weeks aren’t unusual and anyone willing to take the hours will be cashing in big time at the end of the season. But the hours are generally predictable, which can make all the difference for some workers.
Installation work is often seasonal. Most people don’t schedule major replacement work when temperatures are at their peak highs or lows when they need to be relying on a functioning system, so these jobs are usually scheduled during the shoulder seasons. And for new construction, many regions have a similar pattern, where major jobs are planned to take place during good weather.
Specialization Is Common For Installers
Actual installation tasks can vary enormously depending on the region and type of system you are working with. Residential HVAC installations tend to have relatively little variability; in warm regions of the country, these will tend toward heat pumps or air conditioning units, with split systems that put the compressor unit outside and evaporator and fan apparatus inside. In colder areas, furnace installations will put you into a lot of basements and require running pipes or ductwork.
Commercial installations are much more variable. In addition to the demands of climate, large buildings almost all have highly customized systems. Increasingly, they have to be integrated closely with Building Management Systems (BMS) which can handle everything from heating and cooling zones to lighting and security controls.
Commercial installers might specialize in:
All these different specialties can result in very different types of work. Whether it’s welding pipes in tight spaces or working with crane operators to place massive HVAC units on office tower rooftops, the experience will be unique.
The economy of the region also factors heavily into the type of installation work being done. When business is booming and new buildings and houses are going up, installers enjoy the freedom and space of an uninhabited construction site. It’s easy to run ductwork, control wire, piping, and electrical feeds through building framework without walls and insulation in the way.
But in other areas, rising costs can drive waves of updates and replacement installations. These jobs are harder both because the timing has to be right—you can’t leave people without heating for a week in the dead of winter—and because the current occupants are actively using the building. They will be in the way and you’ll have to figure out creative ways to work around them.
How to Become an HVAC Installer
By its nature, installation work involves the cutting edge of modern HVAC technology. So installers have to be up-to-date on the latest developments in the industry. Installers need to stay current on training and certifications offered by the manufacturers of systems they are putting in, not to mention more general industry certifications like NATE (North American Technical Excellence).
Installers also need official documentation in many states. States, counties, and cities often license HVAC mechanics and installers across the board. Many require both on-the-job experience and formal classroom education to receive those credentials.
And all technicians that work with refrigeration systems will need an EPA Section 608 certification, which covers the safe handling and disposal of common, environmentally-sensitive refrigerant gases.
A solid technical school or community college training program can provide installers with all those skills, and some of those certs, and put them on the right footing to get started in the field.
Particularly in commercial installation, however, an apprenticeship may be the most reasonable path into the industry. Many commercial projects, particularly in new construction, are heavily unionized. Some states, and almost all unions, use an apprenticeship model to train and bring new installers into the industry. This can involve up to five years of supervised on-the-job experience and hundreds of hours of classroom training.